Overview
A serial number is a unique code assigned by the manufacturer to identify an individual unit of inventory. Tracking the serial numbers can help prevent fraud with returns. It can also help trace where the unit originated. Sellercloud, along with Receivebridge and Shipbridge, allows you to efficiently manage receiving and shipment processes of unique products by tracking their serials. All information submitted within any of these apps is automatically synchronized and displayed in Sellercloud.
Set up Serials Workflow
You can set all new products to require a Serial Number Scan automatically if you enable a company-level setting Require Serial Number Scan In Scan & Ship. To locate it, navigate to Settings > Companies > Manage Companies > Open a Company > Toolbox > Defaults.
To have the system require a serial of a product each time it is received or shipped, follow the steps described below:
- Access Inventory > Manage Inventory.
- Select the product that is considered to be processed as unique per each item.
- Click the Toolbox, and select Shipping Preferences.
- In the upper right corner, click the Edit option.
- In the Preferences panel, select the Require Serial Number Scan In Scan & Ship check box.
- Click Save to update the product preferences.
- Be sure to also review and configure the Related Client Settings.
Receive Inventory with Serials
You can organize your receivings either from Sellercloud, or via Sellercloud’s Receivebridge – a standalone tool intended specifically for managing your receiving process.
Receive Inventory in Sellercloud
- Access Purchasing > Manage POs.
- Select the PO you want to receive.
- In the upper right corner, click Actions, and select Receive Shipment.
- Indicate receive details, and received quantities.
- Click Receive Items.
- Once processed, click the link in the notification to enter serials.
- Alternatively, switch to the PO page. Click Toolbox, and select Serial Numbers.
- Click Edit.
- In the Serial Numbers panel, expand the appropriate Receiving Session.
- Enter the serials per each received item.
- In the upper right corner, click the Save button.
If your workflow requires often receiving large Purchase Orders containing serial numbers, we recommend enabling the Use Simple Grid For PO Serial Numbers Toolbox Client Setting. When enabled, you will see a simplified grid in the Serial Numbers panel of the PO Toolbox, where entries are not grouped by Receiving Sessions. The Simple Grid is an enhanced version of the default view, which loads faster and supports better filtering capabilities.
Receive Inventory through Receivebridge
Prior to managing receivings in Receivebridge, you should make the relevant adjustments in this tool.
- Refer to the Receivebridge’s Menu > Options. Select the Require serial number input, which is in the General tab.
- Optionally, you can adjust other additional validations on serials, see figure below.
- Once the settings are saved, click Refresh List.
- Filter the list by the requested SKU/UPC, and select the appropriate PO.
- Click the Scan Purchase Order button.
- Input the SKU number, and click Mark as Received.
- In the dialog box that appears, scan/input the serial number of the specified SKU. Click OK.
- When finished scanning all the received items, click Save Receive Data.
- The notification on successful process completion will appear. Inventory calculation will be processed by a queued job and can be seen in Sellercloud.
Ship Inventory with Serials
You can organize your shipments either from Sellercloud directly, or via Shipbridge – a standalone tool intended specifically for managing inventory shipment processes.
Ship via Sellercloud
- Access Orders > Manage Orders.
- Select the Order to be sent to a customer.
- Click Toolbox, and select Serial Numbers.
- Click Edit.
- In the Serial Numbers panel, expand the appropriate SKU and enter a unique serial number for each item in the list. Sellercloud’s mobile application supports barcode scanning using your phone’s camera.
- Alternatively, to open the Serial Numbers panel, click Actions, on the product’s home page. Select Manage Serial Numbers.
- When the unique products in an Order are provided with their serials, go to the Order’s Actions menu, and select Ship Order.
- Alternatively, click Toolbox on the requested Order page, and select Shipping. Click the Ship Order icon that is in the Shipping Details panel.
If an Order has not been yet paid, the Allow Shipping Without Payment option has to be enabled to make the Ship Order option appear.
Ship via Shipbridge
Prior to managing shipment processes in Shipbridge, you should make the relevant adjustments in this tool.
- Refer to Shipbridge’s Menu > Options.
- Switch to Scan and Ship tab.
- Select the Require serials to match PO option.
- Select the Require Serial Number validation option.
- Once the settings are saved, click Refresh List, in the upper right.
- Filter the list by the requested SKU or other parameters, and select the appropriate Order.
- Click the Scan and Ship button and follow the instructions of the wizard.
Track Serials when Making Product Movements across Warehouse
Tracking serial numbers is also valuable when transferring inventory between different warehouses. By associating a serial number with each unit, you can verify whether your units have been shipped or moved to another location. To see the history of product transfers, follow the below steps.
- Access Inventory > Manage Inventory.
- Select the product the unit of which you want to track.
- Click Toolbox, and select Serial Numbers.
- Use the top filters, to find a certain unit, or to review all the units in a specific warehouse.
Export Serials in Bulk
To download a list of inventory arrivals with serials specified, follow the steps described below.
- Access Inventory > Inventory Arrivals.
- Select the arrived SKU(s) to be exported.
- In the bottom right, click the Actions menu, and select Export With Serials.
Related Client Settings
CLIENT SETTING | DEFINITION |
Show Serial Number on Order Details | When selected, the Serial Number field appears on the Purchase Order page |
Show Serial Number on Invoice Details | When selected, the Serial Number field appears on the Invoice page, within the Description box |
Enable Serial Number validation | This controls the validation process within Sellercloud. It checks whether the serial numbers match the serial numbers assigned to units when they were received on a Purchase Order.
When this setting is enabled, it will prevent users from deleting serial numbers on the manage product serials page. Alternatively it should be managed on the purchase order. The Validate Serial Globally sub-setting is used in Skustack to always prompt you to scan serial numbers for any of the following:
|
Enable Product Serial number length validation | Enables and sets a default length for a validation message. The length can be adjusted on the product page, within the Shipping Preferences. |
Enable Order profit and loss by serial numbers | When a serial is received on a PO, that specific price will be stored and used on the P&L when that unit is sold |
Transfer Serial numbers while transferring inventory between warehouses | When a SKU-to-SKU transfer is done for a unit, the serial number of that specific unit can be transferred as well in order to preserve history and will allow for resale of that unit. |
Enable Serial Number Management | Allows serial number addition and edit from the Order Details page by going to Action > Manage Serials |
Use Simple Grid For PO Serial Numbers Toolbox | Controls the look of the Serial Numbers panel in Purchase Order > Toolbox > Serial Numbers. When disabled, serials are grouped by receiving session and can only be viewed if you click the arrow to expand the dropdown. With this setting enabled, you will instead see a simplified grid, which allows for easier filtering and loads quicker when there is a large number of serials. |
A serial number is a unique code assigned by the manufacturer to identify an individual unit of inventory. Tracking the serial number can help prevent fraud with returns. It also can help trace where the unit originated. Serial number management enables you to:
- Assign serial numbers to products as they are shipped out – The serial number saves to order and allows you to verify returned units.
- Assign serial numbers to products as they are received on a PO – The serial number saves to the PO and allows you to check the origin of a unit.
- Validate that the serial numbers match the serial numbers assigned to units when they were received on a purchase order – This completes the cycle. If a defective item is returned you will be able to trace the originating vendor.
- View movement history of a serial number
- Reject serial number that are not a defined length – This safeguard feature can help prevent inaccuracies when recording the serial number.
There are several Client Settings that manage the workflow of serial numbers:
- Enable Serial Number validation – This controls the validation process within SellerCloud as explained in item 3, above. There are separate settings required for shipping through ShipBridge and receiving through ReceiveBridge. Please note that the SB and RB settings work independently of the client setting; the client setting does not need to be enabled for the serial number to be validated in SB or RB. See below in the workflow.
- Validate Serial Globally sub-setting – Use this option for Skustack to always prompt you to scan serial numbers for any of the following (excludes Receiving, which is controlled by the client setting Require serial scan when receiving):
- Bin-to-bin transfers
Bin/Warehouse adjustments
Warehouse-to-warehouse transfers (the picking and receiving process)
SKU-to-SKU SKU transfers
Kit Assembly picking/prepping
Bin cycle counting
Credit Memo picking
FBA Picking
FBA Box content packing
PutAwayList
One-way transfers
- Bin-to-bin transfers
- Validate Serial Globally sub-setting – Use this option for Skustack to always prompt you to scan serial numbers for any of the following (excludes Receiving, which is controlled by the client setting Require serial scan when receiving):
- Enable Product Serial number length validation – Enable and set a default length. The length can be adjusted on the product level in the Shipping Preferences page.
- Enable Order profit and loss by serial numbers – When a serial is received on a PO, that specific price will be stored and used on the P&L when that unit is sold.
- Transfer Serial numbers while transferring inventory between warehouses – When a SKU to SKU transfer is done for a unit, the serial number of that specific unit can be transferred as well in order to preserve history and will allow for resale of that unit. This setting should be enabled in conjunction with Enable Serial Number validation
- Enable Serial Number Management – Allows serial number addition and edit from the Order Details page by going to Action > Manage Serials.
- Show Serial Number on Order Details – Displays serial number on Order Details page where applicable.
- Show Serial number on Order invoice – Displays serial number on standard invoice where applicable.
Serial number workflow
Enter Serial Numbers When Receiving a PO or a Credit Memo.
- When receiving a PO or Credit Memo in SellerCloud:
- Open the action menu and click Manage Serial Numbers
- On the following page scan the serial numbers into the grid.
- If there are multiple SKUs in the purchase order, select the SKU from the drop down menu and enter the serial numbers of that SKU.
- When receiving a PO in ReceiveBridge: Set requirements to input a Serial Number for specific items. This requirement can be set in SellerCloud.
- Set requirements to input a Serial Number for specific items. This requirement can be set in SellerCloud. Navigate Inventory > Product > Toolbox > Shipping Preferences.
- Check the option to Require serial number scan in Scan & Ship and save the preferences.
- Open the menu in ReceiveBridge and click Options.
- Open the “General” tab and enable the setting to Require Serial Number input. You may also want to enable Require Unique Serial Number. When enabled, RB will only accept a serial number that was not yet scanned in this PO. It will also not accept a serial number input if it’s equal to a UPC in the PO. This helps prevent scanning the UPC barcode instead of the serial number, as they are often in close proximity. Save your settings.
- When scanning items during receiving, you will be prompted to scan the serial number. By scanning the serial number, the serial number will be entered on to the purchase order on the Manage Serial page.
Tracking serial numbers as orders are shipped
- When shipping through ShipBridge:
- Navigate Inventory > Product > Toolbox > Shipping Preferences.
- Check the option to Require a serial number when using Scan and Ship and save the preferences.
- When shipping an item using the Scan and Ship, you will be prompted to input the serial number.
- To require the serial number to match serial numbers that were entered when the units were received, open Menu > Option > Scan and Ship. Enable setting Require serial number to match PO.
- When manually marking order as shipped in SellerCloud:
- Open the action menu and click Manage Serial Numbers.
- Enter the serial numbers for every SKU in the order.
Viewing serial number movement
- Product Serial Report – When client setting Enable Serial Number validation is active, the Product Serials Report tab will display under Inventory tab. Search by serial number to see the movement from PO to order to RMA.
- To view the serial numbers on the order form and have it printed on the invoice, enable the relevant client settings noted above. The serial number will appear on the order form below the Product ID, and on the invoice in the description box.
- Search order by serial number using the Serial Number filter in the Advanced Search tab.
- When receiving the return in ReceiveBridge, the serial number will display in the grid when scanning the return.
- To trace from which vendor you purchased the item, open the Purchasing tab and search the purchase orders by serial number.
- To generate a report of all serials received based on a vendor or manufacturer:
- Navigate Inventory > Inventory Arrivals.
- Select a vendor or manufacturer
- Select the purchase orders.
- Open the action menu and click Export with Serials. The file will show one row per serial number.
- Tracking serial numbers is also valuable when transferring inventory to an FBA warehouse. By associating a serial number with each unit, you can verify whether your units were shipped, which can help when making an insurance claim in the event that the shipment got lost. Read how to add serials to FBA shipments here.
Exporting serials in bulk
You can select multiple products from your Inventory Management screen and export their serials from the Action Menu > Export Product Serial Number.
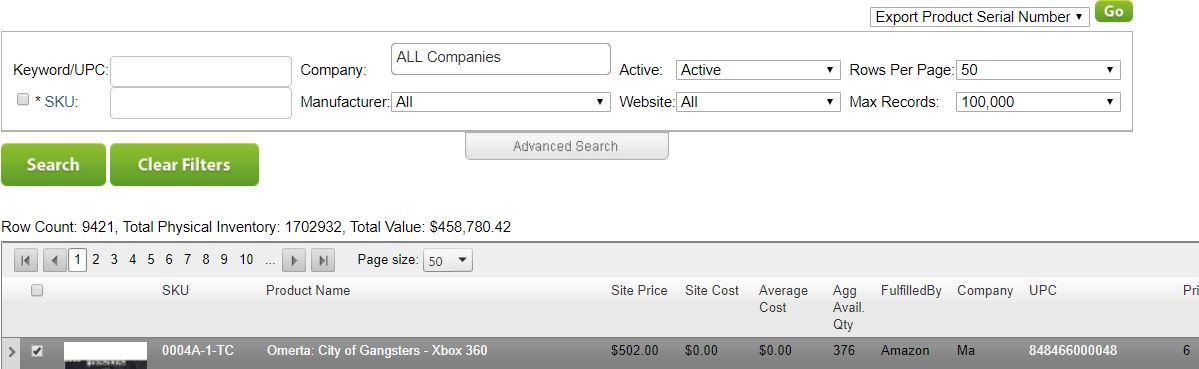